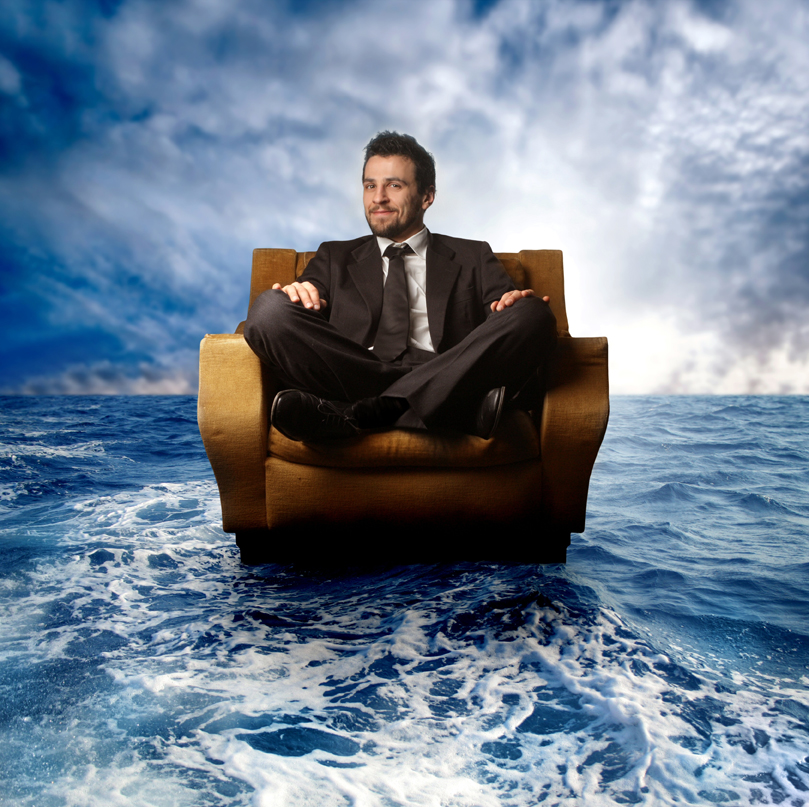
It is tempting to think of supply chain risk in terms of a catastrophic and unpredictable event; but potential threats are often closer and more preventable than many people think, as Andrew Kinder explains.
Even without the recent turbulence in the capital markets, executive minds were already spinning with the relentless onslaught of events in the past year that have threatened to disrupt their continuity of supply.
An expanding list of globally scarce resources, rising energy and fuel costs, volatile and unpredictable demand and increased international regulation are each taking their toll on profitability. And this is without consideration of geopolitical events, terrorism and natural disasters that drive chaos into the best strategic supply chain plans overnight. For executives in manufacturing and distribution, tomorrow’s source of disruption will be another lesson in the management of uncertainty.
To effectively manage this uncertainty, executives must analyse and find actionable answers to the following key questions:
- Have the key sources of risk been identified and their impact assessed?
- Has the organisation built chaos-tolerant supply chains that can absorb the knocks?
- Is risk management seen as a one-off exercise, initiated in response to an unexpected event, or are employees actively building risk mitigation into their everyday activities?
This article examines some of the key sources of risk and practical steps that organisations can take to mitigate supply chain disruption.
Identifying the real sources of risk
A common response when executives are asked about the risks in their supply chain is to think in terms of headline-grabbing disasters: factory explosions, earthquakes, freak weather conditions, the loss of the container ship carrying three months’ supply of your product, etc. Such events are, by their nature, infrequent and unpredictable, leading many to bypass risk management as being too difficult to address meaningfully beforehand. “We’ll deal with it when it happens,” would be a common reaction.
But the reality is that the real risks in your supply chain are closer to home than you think and are altogether more predictable and in your control than imagined.
As a case in point, one Infor customer based in New Orleans faced the ultimate disaster in the form of Hurricane Katrina. The event was indeed a disaster for the region, for the company call centre and distribution facilities, and for the impact on its associates. But in supply chain terms, it proved to be minimal. The company experienced no system downtime, lost less than three per cent of network capacity for a few weeks, and, because of the nature of the cleaning products it distributes, actually recorded some of its highest sales in the weeks that followed.
There are several lessons from this example. The first is that even natural disasters can be anticipated and planned for. Given the locality of the business, the potential impact of hurricane damage was not unimagined, and the organisation had prepared plans that included actions such as rapid rerouting of supply from other US distribution centres, switching from owned transport to common carriage and anticipating spikes in demand for certain product lines with the ability to switch supply sources quickly to meet requirements.
But the bigger discovery is that if something on the scale of Katrina did not constitute a major supply chain risk to the organisation, then what did?
Risks are more predictable than you think
In a recent Infor Executive Summit, executives were asked about the sources of risk. The number one risk was reported as supplier failure. Manufacturing disruption, logistics failure, IT failure and rising fuel and energy costs completed the top five. Natural disasters polled last.
The findings are in keeping with the results of a much wider study from AMR Research, which reported supplier failure as the number one risk factor for 28 per cent of firms polled [source: Managing Risk in the Supply Chain, January 2007].
Returning to the New Orleans-based company, events having a much greater long-term impact on their supply chain were reported as the following:
- Rapid growth, year over year for more than eight years
- Expanding and opening new facilities
- Massive increase and churn in product range
- Adding new, large customers
- Substantial changes in the supplier base
- Changing or implementing IT systems.
The interesting thing about these risks is that they are all entirely predictable and largely within the control of an organisation when compared with other external factors such as natural disaster and geopolitical or macroeconomic factors.
Building a chaos-tolerant supply chain
There is much at stake in terms of the millions of dollars that flow through the supply chain, the impact on long-term competitiveness through failure to deliver, or the damage to brand reputation from a failed product launch, or worse, a product recall through material defect.
What can organisations do to mitigate risk? And how can a well-prepared risk migration strategy be usefully turned into a competitive weapon that enables companies to take an opportunity from an unexpected event? Here are some strategies and examples.
Build risk identification into everyday operations:
Managers need to visualise and understand what potential sources of risk affect their part of the business and formalise the identification of these into daily practices. Risk management is like quality management or the sustainability strategy—it needs to be pervasive. If the assessment of risk is a different function or a separate department, then it will fail to address the everyday sources of risk, where the evidence suggests their impact is highest.
An example taken from another Infor customer involves strategic sourcing. The organisation mapped out its supply chain right through the multiple levels of suppliers to identify the critical raw materials for which there are few global sources. They recognised that availability of these resources is scarce and that global demand has the potential to outstrip supply, with the potential to catastrophically disrupt their own ability to satisfy customer demand. Once identified, they were able to address the risk in multiple ways including duel sourcing, reserving capacity with the suppliers in advance and working with product development to find alternative ways of designing their products without dependence on those critical resources.
Use supply chain modelling and scenario analysis to quantify alternative plans:
With the risks identified, it becomes possible to assess alternate strategies and their impact and cost to the business. Supply chain modelling and network design are tools that can provide valuable assistance in this area. For example, an organisation with an extended supply chain could easily model the impact of fuel increases on transportation costs and test out different sourcing strategies to adopt in the event of a further doubling in oil prices. In the face of rapid expansion, they can quantify how much extra capacity they need and where to locate new manufacturing and distribution capacities or how to absorb capacity among remaining plants in a consolidation process. One US-based food company tells how they regularly switch capacity between their various facilities in response to differential energy prices across several states, maintaining margins in the face of rising energy costs and seeking competitive advantage over more static supply chain organisations.
New product developments can identify and avoid globally scarce materials, or those which have different legislative requirements placed upon them between different countries, thus lowering compliance risk. As companies increase use of outsourced manufacturing sources and suppliers are developing more value products, supplier compliance capabilities, levels and countries in the supplier’s supply chain can expose hidden risk. Product lifecycle modelling can speed time to market, reduce compliance risks and reduce the risk inherent in being late into a developing market.
There are technology solutions available that make it easier to assess the impact of risk on a business’s supply chain and evaluate alternate strategies to enable managers to make the final assessment of whether any pre-emptive strike is, on balance, a risk worth taking to the organisation.
Value supply chain agility over efficiency:
A number of organisations have built their risk mitigation strategies on the principle of supply chain flexibility. They accept that events move quickly, whereas turning supply on and off can often seem like turning the proverbial tanker. Efficiency in supply chains is frequently built on predictability, repeatability and a solid supply chain network. When the unexpected occurs, such supply chains can be slow to react. The fashion industry is one of the first to recognise the benefits of agility and has coined the term ‘fast fashion’ to describe supply chains that can deliver from design to shelf in weeks, responding to consumer trends multiple times in a season. This provides a massive competitive advantage and significantly reduces supply chain risk to those practicing fast fashion in meeting demand driven by an unusually wet summer, or reacting rapidly to a design that is suddenly made the ‘must-have accessory’ from a TV personality or news item.
Improve responsiveness through smart alerting:
Supply chain leaders know that the sooner an unplanned event can be detected, the greater the opportunity to minimise its impact—or to maximise its benefit. For example, early notification of the promotional success of a product on a retail shelf can pass right through the tiers of the supply chain to profit from the peak. Equally, early detection of a poorly performing product launch can save millions in the avoidance of obsolete inventory or poorly used capacity. There are infinite numbers of opportunities for real-time detection capabilities that can be the eyes and ears of the supply chain, continuously and silently monitoring for unusual events: missed shipments, late orders, data discrepancies and stock write-offs. It does not represent a preventative measure, but early identification and action are a valid risk mitigation strategy.
Create a framework for continuous and formal assessment of supply chain risk:
There is no one single approach or technology in dealing with risk. It varies from industry to industry and across strata of supply chain maturity. What is needed is to make risk identification, with a qualitative and quantitative assessment of alternatives, a formal part of the supply chain process. Some organisations report that this framework has become part of their overall executive sales and operations planning process—increasingly known as ‘integrated business planning’. Since such a process is frequently driven by supply chain functions, it is a suitable starting point for introducing risk identification into the overall business plan that the executives are signing up to.
Conclusion
Supply chain risk management is an increasingly important initiative for business as a proactive response to turbulence in today’s fast-paced business environment. While it is tempting to perceive risks as unplanned, unexpected events that companies can do nothing about until they happen—the reality is that sources of strategic supply chain risk are much closer to home and easier to identify and predict than at first apparent. Managers must formalise their approach to risk identification in their everyday activities and catch potential problems before those events become catastrophes. Technologies are available to help identify, quantify and build scenarios to test alternative action plans as preparation if an event occurs, as well as improve the ability to sense and respond quickly to events and minimise their impact.
Forcing oneself to think in terms of potential sources of risk, their likelihood and what to do about it in its eventuality is not easy—but doing so is the only way to allow risk to be mitigated, rather than just responded to. A crystal ball would help, but until these are market tested and readily available, other strategies must prevail.
Andrew Kinder is director of product marketing for supply chain management at Infor. For more information, visit www.infor.com.